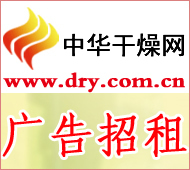
On April 16th, the first set of 200,000-ton-per-year acetic acid esterification hydrogenation to ethanol industrial demonstration unit was established in Southwest China Chemical Research and Design Institute's own patented technology, and its partner Henan Shunda Chemical Technology Co., Ltd. officially started construction. The project can not only replace the traditional food fermentation ethanol route, but also can extend the acetic acid industry chain to solve the problem of excess production of acetic acid, to provide new support for the acetic acid industry.
The project adopts the route of esterification and hydrogenation of acetic acid. No corrosive substances are generated in the reaction process, and the equipment requires low material and investment. At the same time, the project team developed a non-precious metal catalyst with low cost, good activity, excellent performance, a conversion rate of up to 97%, and a selectivity of more than 98% for ethanol. In addition, the production device can obtain acetate and ethanol products at the same time, which not only realizes the diversification of products, but also the ethanol product reaches the fuel addition standard (absolute ethanol).
According to reports, Southwest Institute began research and development of acetic esterification hydrogenation to ethanol in 2008. It has completed small-scale trials, single-tube trials and pilot tests, and developed a new acetate hydrogenation catalyst to explore the best acetic acid. Ester hydrogenation process conditions, and apply for six national invention patents, the formation of a new process and new technology with independent intellectual property rights. It is reported that the total investment of the project is 500 million yuan, and it is expected to be completed and put into production by the end of 2013. The annual sales income after the project is put into production will be 1.3 billion yuan, and the annual profit will be nearly 70 million yuan.
At present, China's chemical industry consumes about 3 million tons of industrial-grade ethanol each year, and the annual growth rate of market demand is 8% to 10%.
In 2011, China's fuel ethanol consumption was 1.8 million tons. According to relevant national plans, China's fuel ethanol utilization will reach 10 million tons by 2020.
In addition, China has now become the largest producer of acetic acid . In 2011, China's acetic acid production capacity exceeded 7 million tons, acetic acid production was 4.25 million tons, the average operating rate of acetic acid plants was only 60%, and apparent consumption was 3.56 million tons. It is estimated that by 2015, China's acetic acid production capacity will exceed 10 million tons. At that time, the consumption demand of acetic acid will reach 5.38 million tons, and consumption will still be mainly concentrated in poly(terephthalic acid, vinyl acetate, acetate, chloroacetic acid, diketene, pesticides, In the fields of pharmaceutical intermediates and other fields, the contradiction between excessive growth of production capacity and lagging behind in demand will be more prominent, and the emergence of the process of acetic esterification hydrogenation to ethanol can be alleviated.
BMC Special Injection Molding Machine
AOTAI Servo Driving System
1. Show High Precision:The accurate injection positioning,pressure, speed ang pressure maintaining, to ensure the ensure the repeatability error of injection accuracy less than 0.3%to achieve precision molding.
2. Super Energy-Saving Features:Compared with standard injection machine, the energy saving rate can reach 40%-70% for the same plastic production.
3. High Efficiency:Compated with standard machine,the total efficiency can increase by 10% and dragging capacity is can increase by 18%
4. High Respomse System:The system acceleration and deceleration performance is quite agile and force &speed regulation is very sensitive. The sampling processing speed can reach 100KHZ and system quick start time can reach 0.05s.
5. Maintain Stability and Reliability:The pressure or speed is stable and switch of pressure maintaining is smooth and accurate.
6. Low Oil Temperature:Avoid high pressure unloading and low oil temperature situation during operation. Improve the operation performance,promote using efficiency and save a large quantity of coolong water.
BMC Injection Molding Machine is equipped with thermosetting physicochemical components which is specialized for BMC material. and it has sysytem optimization module which is composed of specific charging high torque hydraulic motor for charging and special injection hudraulic cylinder etc.
J system characteristic
Design and reseatch on high energy-saving injection molding machine has been regarder as our National Torch Plan and we are the earliest company who is engaged in this project. Servo motor can disctate different machine action according to product workmanship requirement. To inqut data into the controller and instruct different workload demand of every machine action quickly. The linearity of servo driving system operational process keeps good tracking with workmanship instrucion. In this case, the system pressure and flow becomes a closed loop, which achieves high machine performance & high energy-saving by 40%-70%. With this high-response system, the efficency of machine can be more than 98%.
High combination device
1. Imported brand controller
Imported options: mainly KEBA and B&R,Display the concept of high response & multfunction people-oriented control
2. CE standard system & series
hybrid system & machine series, which is honored with CE certificate, to improve the safety rate during machine operation
3. Overlap movement high speed system
Ejection or plasticizing when mold opening & clamping, to increase machine cycle and achieve high efficiency
4. High efficiency non-standard power/capacity expansion systm
Add driving function on standard machine power, so to increase operation cycle obviously & achieve super quality and high efficiency.
5. High speed acceleration/accumulator unit
Suitable for the production of thin-wall& fast molding products, so to meet the processing requirements of precision & high difficulty products
6. High precision injection unit pressure sensor device
Improve system pressure real time cycle during injection unit operation, so to realize the closed-loop effect of injection/holding pressure and pre-plasticizing & back pressure
7. High precision injection servo valve/closed-loop device
Applicable to processing requirements of extremely precision high end products, so to increase injection repeat accuracy efficiently
8. Single cylinder fast injection device
Appropriate for 360T(or below) machine is clamping unit to match single cylinder high injection molding, so to ensure the production of ultrathin-wall products ,and realize super quality and high efficiency.
9. Optimum function combination of clamping & injection
Suitable for the pertinent special products by nonstandard and optimum customized combination of clamping unit & injection unit machine, so to reach most suitable application of optimum mass production.
BMC Special Injection Molding Machine
BMC Special Injection Molding Machine,Big Plastic Injection Machine,Ball Pen Making Machinery,Automatic Injection Machine
NINGBO BEILUN ALLWAY MACHINERY CO., LTD. , http://www.aotai-machinery.com